High-Performance Special Purpose Sensors for Accurate Measurement | Micro-Measurements
Micro-Measurements offers a range of special sensors designed to meet the precise demands of professionals working in the automotive, aerospace, civil engineering, and industrial sectors. Our sensors are engineered to handle challenging environments, including high magnetic fields, concrete structures, and areas requiring crack detection. Whether you're measuring residual stress, monitoring crack propagation, or conducting shear modulus testing, our comprehensive range of solutions ensures high accuracy and reliability. Micro-Measurements is your trusted partner for accurate, durable, and application-specific sensor technologies that provide critical insights into structural performance.
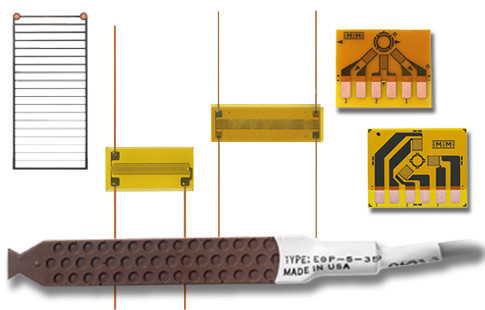
Types of Micro-Measurements Special Sensors:
- Residual Stress Strain Gages: Precision sensors designed to measure stress in a variety of materials under real-world conditions.
- Magnetic Field Gages: Ideal for use in environments with strong electromagnetic interference, providing accurate strain readings in high magnetic fields.
- Weldable Gages: Durable, easy-to-install strain gages for long-term monitoring of welded structures and components.
- Shear Modulus Testing: Accurate tools for evaluating the mechanical properties of composite materials through Iosipescu shear testing.
- Concrete Embedment Gages: Engineered to measure strain within concrete structures, ideal for long-term monitoring of bridges, buildings, and other civil infrastructure.
- Crack Detection and Propagation Sensors: Advanced sensors designed to detect the initiation and growth of cracks in critical structures, enabling preventative maintenance.
- Displacement Sensors: High-precision sensors for measuring linear displacement in mechanical systems.
- Temperature Sensors: Bondable sensors with thermal mass similar to strain gages can be used to measure and compensate for temperature changes during strain measurements, ensuring accuracy across environments.
Industry Applications for Special Use Sensors
In the automotive sector, residual stress strain gages (gauges) and crack propagation sensors play crucial roles in maintaining structural integrity and safety. For automotive applications, the ASTM E837 standard, known as the "Standard Test Method for Determining Residual Stresses by the Hole-Drilling Strain-Gage Method," provides a semi-destructive, industry-accepted technique to measure residual stresses in vehicle components. Similarly, in aerospace, crack propagation sensors are essential for monitoring stress within aircraft fuselages and wings, safeguarding their structural reliability over prolonged periods of use in high-stress environments.
In civil engineering, monitoring tools like concrete embedment gages, displacement sensors, and temperature sensors ensure the durability and safety of infrastructure and equipment. Concrete embedment gages track strain in structures like bridges and tunnels, offering data that informs maintenance decisions for long-term health and safety. In industrial settings, displacement and temperature sensors enhance manufacturing precision, helping detect early signs of machinery wear or fatigue, thus optimizing equipment operation and preventing costly downtime.
For Our Full Range of Special Use Sensors
RESIDUAL STRESS GAGES
The most widely used practical technique for determining residual stresses is the hole-drilling strain gage (gauge) method. A specially configured strain gage (gauge) rosette is bonded to the surface of the test object. A small, shallow hole is introduced into the structure, through the center of the gage, using a precision drilling apparatus. Strains near the hole are measured, and the relaxed residual stresses are computed from these measurements.
Learn more about the general theory of making residual stress measurements in Micro-Measurements Tech Note TN-503, “Measurement of Residual Stresses by the Hole-Drilling Strain Gage Method.”
CRACK DETECTION AND CRACK PROPAGATION
CRACK DETECTION • CRACK PROPAGATION
CD-Series Crack Detection Gages are expertly designed to provide a convenient, economical method of indicating the initiation presence of a surface crack.
The CPA, CPB, and CPC patterns consist of a number of parallel resistor strands, when broken indicate the rate of crack progression or propagation. When bonded to a structure, progression of a surface crack through the gage (gauge) pattern causes successive open-circuiting of the strands, resulting in an increase in total resistance.
MAGNETIC FIELD STRAIN GAGE
Intense electromagnetic fields with steep gradients in field strength can cause troublesome noise in strain gage (gauge) circuits. In severe magnetic environments, with low signal levels, the noise amplitude may be several times larger than the strain signal from the gage (gauge). Micro-Measurements H-Series non-inductive strain gages (gauges) have been specially designed to minimize noise pickup in the gage (gauge) grid due to electromagnetic fields. H-Series strain gages (gauges) consist of two identical grids, with one stacked directly above and insulated from, the other, an arrangement that allows noise voltages to be self-cancelling.
H-Series strain gages (gauges) are very successful in fusion research applications and similar environments with flux densities to 50,000 gauss.
DISPLACEMENT
Cable-Extension Displacement Sensor (CDS) • Linear Displacement Sensors (HS Series)
The Micro-Measurements Cable-Extension Displacement Sensor (CDS) provides a voltage signal linearly proportional to the extension of a retractable stainless steel cable. Used for indicating the displacement of the test structure, member or part to which the cable is attached, installation is quick and easy.
Micro-Measurements Linear Displacement Sensors (HS Series) use a fully active 350-ohm strain-gage bridge to sense spindle displacement, giving infinite resolution and excellent linearity. They are compatible with all standard strain-gage instrumentation with bridge excitation from 2 to 10 volts. With a selection of models having full-scale ranges from 1/4 inch (5 mm) to 4 inch (100 mm), Linear Displacement Sensors feature a unique design that produces maximum operating forces of less than 1 lb. (4.4 N).
SHEAR MODULUS
Shear Modulus Sensors are specifically designed to accommodate the unique specimen geometries and strain-field distributions encountered when testing composite materials for shear properties. Two gage (gauge) sizes are available, in both planar and stacked shear rosette configurations, for the Iosipescu and Compact test specimens.
Determining shear modulus requires extracting an average shear-strain value from the non-uniform strain field present in both specimen sizes. Since strain gages (gauges) have the unique characteristic of integrating the surface strain field under their grids, average specimen strain is automatically obtained by spanning the entire length of either specimen’s test section.
TEMPERATURE (RTD)
Micro-Measurements’ high-precision resistance temperature sensors use nickel rolled foil grids. For temperature compensation circuits used in full-bridge transducer applications, Micro-Measurements offers and are also available in Balco® alloy or copper foil grids. These temperature sensors are bonded to structures using standard strain gage (gauge) installation techniques, and can measure surface temperatures from –452° to approximately +500°F (–269° to +260°C). Because of their extremely low thermal mass and the large bonded area, the sensors follow temperature changes in the structural mounting surface with negligible time lag.
CONCRETE EMBEDMENT
The EGP-Series Embedment Strain Gage is specially designed for measuring mechanical strains inside concrete structures. The sensing grid, constructed of a nickel-chromium alloy (similar to Karma), has an active gage (gauge) length of 4 inch (100 mm) for averaging strains in aggregate materials. A rugged 5 inch (130 mm) outer body o resists mechanical damage during pouring, matches stiffness of the concrete, thus eliminating the presence of an introduced ‘void’ in the material, and provides sustained protection from moisture and corrosive attack.
PRESSURE PULSE
Micro-Measurements offers a large selection of gages (gauges) for shock wave studies, manufactured from specially treated shunt stock Manganin foil. Manganin gages (gauges) are used extensively in high-pressure shock wave studies ranging from 1 to over 400 kilobars (1 bar = 14.5 psi = 100 000 N/m2). In conventional applications, the gage (gauge) is bonded between two flat metallic or polymer plates. The ultrathin construction offers several advantages over the wire type, including:
- Improved repeatability from gage to gage
- Faster response times
- Smaller, high resistance grids
- Minimal distortion of the pressure wave
Discover how our special purpose sensors can enhance the precision and reliability of your strain measurements. Contact our team today to learn more about our solutions, request a demo, or visit our comprehensive guide to special sensors for dynamic and static strain measurement applications.
Contact Our Special Use Sensors Experts

RESOURCES
Learn about our stress analysis products, watch informative videos, and explore our large knowledge base.
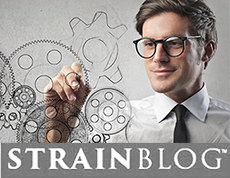
STRAINBLOG
Questions and answers on the go! Listen to Micro-Measurements experts explain the many facets of strain gage (gauge) technology.
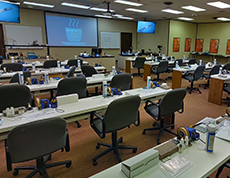
TRAINING
Benefit from an extensive series of regularly scheduled, hands-on technical workshops and short courses.
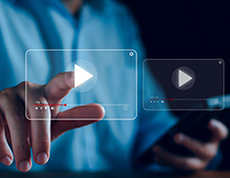
VIDEOS
Explore our extensive collection of tutorials and informational videos on a variety of strain measurement topics.